RUGOSIDAD.
RUGOSIDAD
Aunque durante mucho tiempo la medición de
la rugosidad no fue considerada como una rama de la metrología, en la
actualidad es un requerimiento importante debido al reconocimiento
creciente de la importancia y necesidad de esta medición.
Una superficie perfecta es una abstracción
matemática, ya que cualquier superficie real, por perfecta que parezca,
presentará irregularidades que se originan durante el proceso de
fabricación.
Las irregularidades mayores
(macrogeométricas) son errores de forma, asociados con la variación en
tamaño de una pieza, paralelismo entre superficies y planitud de una
superficie o conicidad, redondez y cilindricidad, y que pueden medirse
con instrumentos convencionales.
Las irregularidades menores
(microgeométricas) son la ondulación y la rugosidad. La primera pueden
ocasionarla la flexión de la pieza durante el maquinado, falta de
homogeneidad del material, libración de esfuerzos residuales,
deformaciones por tratamiento térmico, vibraciones, etcétera; la segunda
la provoca el elemento utilizado para realizar el maquinado, por
ejemplo, la herramienta de corte o la piedra de rectificado.
Los errores superficiales mencionados se
presentan simultáneamente sobre una superficie, lo que dificulta la
medición individual de cada uno de ellos.
La rugosidad (que es la huella
digital de una pieza) son irregularidades provocadas por la herramienta
de corte o elemento utilizado en su proceso de producción, corte,
arranque y fatiga superficial.
El acabado superficial de los cuerpos puede presentar errores de forma macrogeométricos y microgeométricos.
- La rugosidad superficial es el conjunto de irregularidades de la superficie real, definidas convencionalmente en una sección donde los errores de forma y las ondulaciones han sido eliminados.
Superficie real: Superficie que limita el cuerpo y lo separa del medio que lo separa.
Superficie geométrica: Superficie ideal cuya forma está especificada por el dibujo y/o todo documento técnico.
Superficie de referencia:
Superficie a partir de la cual se determinan los parámetros de
rugosidad. Tiene la forma de la superficie geométrica. Se puede calcular
por el método de mínimos cuadrados.
Perfil real: es la intersección de la superficie real con un plano normal.
La rugosidad de la superficie se determina
considerando la longitud de onda del radar y el ángulo de incidencia.
Una superficie aparecerá ser lisa si sus variaciones de la altura son
más pequeñas que 1/8 de la longitud de onda del radar.
En términos del uso de una determinada
longitud de onda, una superficie aparece más lisa mientras la longitud
de onda y el ángulo de incidencia aumenta.
En imágenes generadas por radares, las
superficies ásperas aparecerán más brillantes que superficies más lisas
del mismo material. La aspereza superficial influencia la reflectividad
de la energía de la microonda.
Las superficies lisas horizontales que
reflejan casi toda la energía de la incidencia lejos del radar se llaman
los reflectores especulares, ejemplos de estas superficies, son el agua
tranquila o caminos pavimentados que aparecen oscuras en las imágenes
de radar. En cambio las superficies ásperas dispersan la energía de la
microonda incidente en muchas direcciones, esto se conoce como reflexión
difusa. Las superficies vegetales causan reflexión difusa y generan
imágenes con un tono más brillante.
Características
Promedio de rugosidad: El valor
promedio de rugosidad en µm es el valor promedio aritmético de los
valores absolutos de las distancias del perfil de rugosidad de la línea
intermedia de la longitud de medición. El valor promedio de rugosidad es
idéntico a la altura de un rectángulo donde su longitud es igual a la
longitud total lm y esto a su vez es idéntico con la superficie de la
suma que existe entre el perfil de rugosidad y la línea intermedia. Rz:
Promedio de la profundidad de la rugosidad en µm (promedio aritmético de
cinco profundidades singulares consecutivas en la longitud de
medición). Los rugosímetros sirven para detectar de forma rápida las
profundidades de la rugosidad en las superficies de materiales. Los
rugosímetros le indican en µm la profundidad de la rugosidad Rz y el
promedio de rugosidad Ra. Tenemos disponibles equipos con un máximo de
trece parámetros de medida. Son aplicables las siguientes normativas en
la comprobación de rugosidad en las superficies delas piezas de trabajo:
DIN 4762, DIN 4768, DIN 4771, DIN 4775. La rugosidad alcanzable de las
superficies las puede ver en DIN 4766±1. Los rugosímetros se envían
calibrados (pero sin certificado). Opcionalmente puede obtener para los
rugosímetros una calibración de laboratorio, incluido el certificado
ISO. Así podrá integrar sus medidores en su control de calidad ISO y
calibrarlos anualmente (a través de PCE o cualquier laboratorio
acreditado).
Rugosidad obtenida: El costo de una
superficie maquinada crece cuando se desea un mejor acabado
superficial, razón por la cual el diseñador deberá indicar claramente
cual es el valor de rugosidad deseado, ya que no siempre un buen acabado
superficial redundará en un mejor funcionamiento de la pieza, como
sucede cuando desea lubricación eficiente y por tanto una capa de aceite
debe mantenerse sobre la superficie.
En el pasado el mejor método práctico para
decidir si un acabado superficial cumplía con los requerimientos era
comparado visualmente y mediante el tacto contra muestras con diferentes
acabados superficiales .Este método no debe confundirse con los
patrones de rugosidad que actualmente se usan en la calibración de
rugosimetros.
Tipos de medición de rugosidad
Los sistemas más utilizados son el de
rugosidad Ra, rugosidad Rx, rugosidad Ry y rugosidad Rz. Los más usuales
son Ra. Rz, Ry. Ra
Los valores absolutos de los alejamientos del perfil desde la línea central.
La altura de un rectángulo de longitud lm,
cuya área, es igual a la suma de las áreas delimitadas por el perfil de
rugosidad y la línea central Rz.
Promedio de las alturas de pico a valles.
La diferencia entre el promedio de las alturas delos cinco picos más
altos y la altura promedio de los cinco valles más profundos Ry.
La máxima altura del perfil. La distancia entre las líneas del perfil de picos y valles.
Medida de rugosidad:
Comparadores visotáctiles. Elementos para
evaluar el acabado superficial de piezas por comparación visual y táctil
con superficies de diferentes acabados obtenidas por el mismo proceso
de fabricación.
Rugosímetro de palpador mecánico:
Instrumento para la medida de la calidad
superficial pasado en la amplificación eléctrica dela señal generada por
un palpador que traduce las irregularidades del perfil de la sección
dela pieza. Sus elementos principales son el palpador, el mecanismo de
soporte y arrastre de éste, el amplificador electrónico, un calculador y
un registrador.
Rugosímetro: Palpador inductivo. El
desplazamiento de la aguja al describir las irregularidades del perfil
modifica la longitud del entrehierro del circuito magnético, y con ello
el flujo de campo magnético que lo atraviesa, generando una señal
eléctrica.
Rugosímetro: Palpador capacitivo.
El desplazamiento vertical del palpador aproxima las dos láminas de un
condensador, modificando su capacidad y con ella la señal eléctrica.
Rugosímetro: Palpador piezoeléctrico:
El desplazamiento de la aguja del palpador de forma elásticamente un
material piezoeléctrico, que responde a dicha deformación generando una
señal eléctrica.
Rugosímetro: Patín mecánico: El
patín describirá las ondulaciones de la superficie mientras la aguja
recorra los picos y valles del perfil. Así se separan mecánicamente
ondulación y rugosidad que son simplemente desviaciones respecto de la
superficie geométrica con distinta longitud de onda.
Rugosímetro: Filtrado eléctrico: La
señal eléctrica procedente del palpador puede pasar a un filtro para
eliminar las ondulaciones, esto es, disminuir la amplitud de sus
componentes a partir de una longitud de onda ᵞ´, (longitud de onda de
corte).
Actualmente los rugosímetros permiten
calcular y tratar numerosos parámetros de rugosidad, compensar la forma
de la pieza o programar la medida.
Medidores de Rugosidad
Visión General
Los medidores de rugosidad, también llamados "medidores de rugosidad superficial", son instrumentos que miden la suavidad (grado de rugosidad) de la superficie de un objeto. Los principales tipos de medidores utilizan sondas o láseres. Convencionalmente, los modelos más comunes utilizan una sonda de diamante, pero los tipos ópticos se han vuelto más comunes, debido a la preocupación de que la sonda de diamante pueda dañar la superficie de semiconductores y objetos similares, durante la medición. Algunos modelos pueden medir superficies planas y curvas. Recientemente, también han aparecido modelos que pueden mostrar una imagen 3D de la forma, en base a los datos medidos de la superficie.Los ejemplos de aplicaciones de medidores de rugosidad incluyen la verificación del desgaste en superficies metálicas, comprobación de superficies cortadas y revisión de acabados de pintura. Con la fabricación de cada vez más componentes electrónicos, utilizando el procesamiento de película delgada, algunos medidores de rugosidad pueden incluso realizar mediciones en el orden de los nanómetros.
Construcción y Aplicaciones.
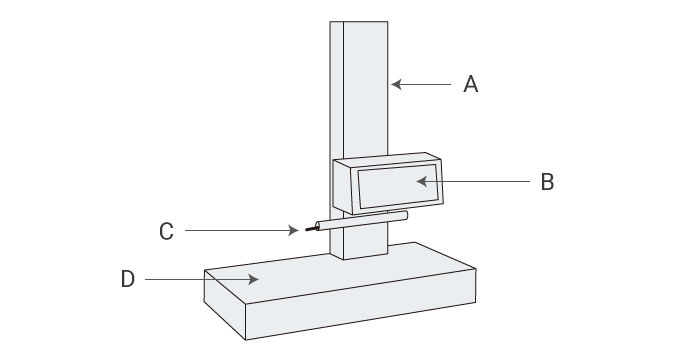
Cómo utilizar un Medidor de Rugosidad.
- Con un medidor de rugosidad de tipo contacto, la rugosidad de la superficie se mide perfilando la sonda sobre la superficie del objeto. En contraste, un medidor de rugosidad sin contacto basado en láser emite un rayo láser sobre el objeto y detecta la luz reflejada para medir la rugosidad.
- La dirección de la medición es la clave para una medición exitosa. Por ejemplo, un producto metálico procesado se mide generalmente de forma perpendicular a la dirección del procesamiento, de modo que el medidor de rugosidad pueda capturar las características de la superficie de manera más confiable.
- La velocidad de medición es también un elemento clave para una medición precisa. La medición se realiza primero lentamente, y luego se aumenta la velocidad mientras no se produzcan fluctuaciones en los valores medidos.
Precauciones de Manipulación.
- Se requiere una calibración periódica para realizar mediciones correctas.